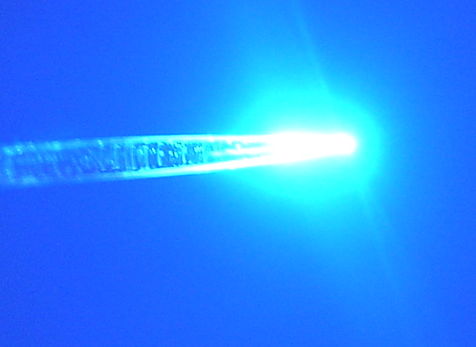
Figure: Taper in 410-μm Higher-Index Fiber. Blue 460-nm light. Taper is 2.0 mm long.
The taper shown above is at the top of a 40-mm shaft of higher-index fiber, polished at the base. Its diameter is 410 μm. We lower the base onto a C460EZ500 blue LED die. This particular LED has output power 27 mW (4.85 mA photocurrent through unbiased photodiode) for forward current 30 mA. Because we were in a hurry, we fastened the fiber to the LED with five-minute epoxy. We bake it in our oven at 60°C and within twenty minutes, the epoxy is fully cured.
We drive 30 mA through the LED. We press our 10 × 10 mm2 photodiode against the side of the fiber, so that the axis of the fiber is a millimeter from the photodiode window. We expect light emitted by the taper more than 20° from the fiber axis, and in a ±80° slice in the radial direction, to enter the photodiode. We see 3.7 mW (0.67 mW photocurrent). We hold the photodiode 15 mm from the top of the taper, and perpendicular to the fiber axis. We now receive most of the light within ±20° of the axis. We see 1.1 mW (0.2 mA photocurrent). Multiplying the first measurement by 2*9/8 and adding the second, we arrive at 9.4 mW total emission from the taper. Assuming 2.2% loss per 10 mm, the power entering the base of the fiber should be 10.3 mW, which is 38% of 27 mW.
We produced four such tapers from two lengths of higher-index fiber polished at both ends. The one we show above is the shortest. We can make them in the same machine with 6 mm of fiber followed by 2 mm of taper. Such a fiber would emit around 10 mW from its tip for 30 mA of LED current.
No comments:
Post a Comment